News
18 mars 2024
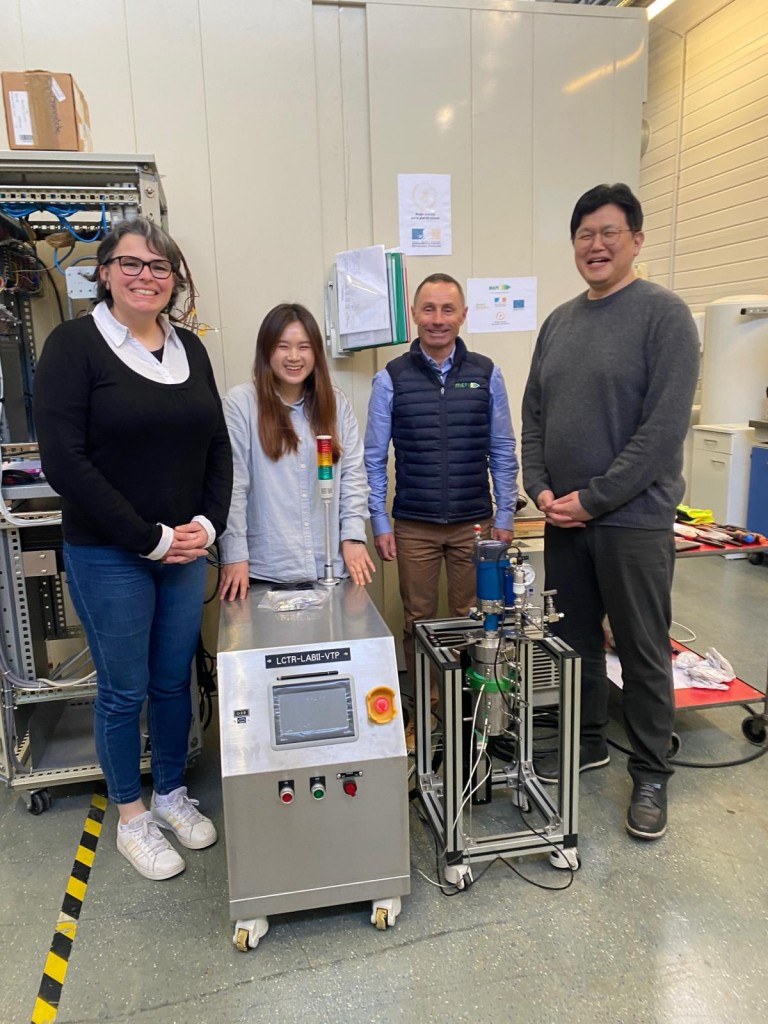
We are very proud to announce a new cooperation with LAMINAR on the development and chemical testing of challenging reactions using a new Taylor Couette reactor. The LAMINAR technology combined with the know-how of MEPI in flow chemistry will allow to deal with longer residence times and solid generation to access new flow chemistries areas.
Laurent Pichon
MEPI Chairman of the Board
Jongpal Hong
LAMINAR CO Ltd CEO
26 juin 2023
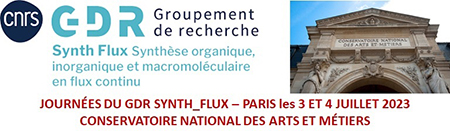
26 mars 2023
April 18th, 2023 : MEPI give a speech at KOREACHEM, KINTEX, Seoul international exhibition centre (Republic of South Korea)

7 décembre 2021
Los siete socios del consorcio TRIPyr se reunirán los días 29 y 30 de noviembre en el Instituto Catalán de de Investigación Química (ICIQ) para celebrar su reunión anual. Los miembros del consorcio compartiránel desarrollo del proyecto y discutirán acciones futuras. Tras la reunión, los socios visitarán las instalaciones de última generación del ICIQ.
El proyecto TRIPyr tiene como objetivo mejorar la calidad del medio ambiente a ambos lados de los Pirineos, transformando residuos industriales tóxicos procedentes de la industria agroalimentaria y de pesticidas en productos de alto valor añadido como polímeros o alcoholes grasos mediante el desarrollo de metodologías basadas en al catálisis.
Ana Aguiar, presidenta de la División de Química Verde y Sostenible de la Sociedad Química Europea (EuCHemS) y experta en química verde y tecnología de CO2 supercrítico de la Universidad Nueva de Lisboa, impartirá la charla “Repensar el uso de CO2 supercrítico”; François Jérôme, del Instituto de Química de Poitiers: Materiales y Recursos Naturales, con amplia experiencia en el acoplamiento de catálisis con tecnologías alternativas, presentará “Tecnologías alternativas para la conversión de biomasa”, y el tercer invitado, Alessandro Zedda, director de Zedda Innovation Consulting & Labs, hablará sobre “Estrategias de monetización para propiedades intelectuales. Conozca el valor de su propiedad intelectual, elija el mejor socio industrial para negociar más y mejores acuerdos de licencia ».
La estrategia de TRIPyr es desarrollar metodologías de vanguardia basadas en catálisis, una herramienta con alta selectividad y economía de átomos y energía, para la transformación de residuos industriales provenientes de la industria agroalimentaria y de pesticidas en materias primas. La transferencia industrial de los procesos estudiados se realizará mediante el escalado de procesos tanto en discontinuo (batch) como en flujo continuo (flow) para la transformación catalítica de residuos grasos industriales de origen animal, así como de residuos halogenados alifáticos, en productos valiosos.
El proyecto se lleva a cabo gracias a una estrecha colaboración transpirenaica entre tres socios académicos: el Laboratorio de Heteroquímica Fundamental y Aplicada (LHFA-CNRS / UT3 Paul Sabatier, Toulouse, Occitania), el Instituto Catalán de Investigación Química (ICIQ, Tarragona, Cataluña) y el Instituto de Ciencias Químicas y Catálisis Homogénea (CHESO, Zaragoza, Aragón); dos centros tecnológicos: la Casa Europea de Procesos Innovadores (MEPI, Toulouse, Occitanie) y la Asociación de Industrias de Navarra (AIN, Cordovilla, Navarra); la PYME Sapoval (Albi, Occitanie) y Ecocène (Pau, Nouvelle-Aquitaine), asociación dedicada a la divulgación pública de la ciencia
——————————————————————————-
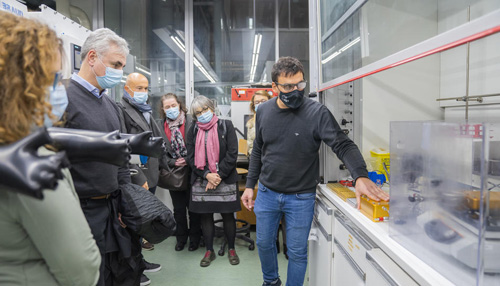
El objetivo es descubrir cómo pueden obtener polímeros a través de residuos para transformarlos en nuevos productos con valor añadido
El Institut Català d’Investigació Química (ICIQ), con su sede en Tarragona, está investigando un nuevo proceso sobre cómo transformar residuos en polímeros, que son los principales componentes del plástico, para entrar en una economía circular sostenible. Este estudio se encuentra en el marco del proyecto TRIPyr , del cual forman parte un total de siete organizaciones de las dos lados de los Pirineos: Catalunya, Aragón, Navarra y el sur de Francia. Estas instituciones tienen el objetivo de mejorar la calidad del medio ambiente transformando algunos residuos industriales tóxicos en productos con valor añadido y atractivos de nuevo por el mercado, como pueden ser polímeros.
Según explicaba en declaraciones al Diari Més el químico líder del grupo de investigación del ICIQ y profesor ICREA, Arjan Kleij, se trata de un proceso con el cual se quiere llegar a una «economía y química circular». «Este modelo sostenible es hacia donde tenemos que ir, porque, si no, las próximas generaciones tendrán una vida mucho más difícil», señalaba Kleij, apuntando al hecho que «actualmente dependemos demasiado del petróleo, y ahora tenemos que caminar hacia las energías renovables».
El TRIPyr se centra en investigar, a través del proceso de catálisis, cómo podemos revalorizar las fuentes de residuos. El objetivo principal es «utilizar estos residuos para transformarlos en algún producto por el cual la industria vuelva a estar interesado, que vuelva a tener un valor añadido,» según el líder del grupo de investigación del ICIQ. De esta manera, sectores como la industria química, química fina, farmacéutica… podrían usar el producto resultante de la catálisis.
Según el químico, a estas alturas hay dos componentes que se encuentran en el centro de esta investigación: el lindano y los ácidos grasos. «El lindano es un producto tóxico, el cual se usaba en forma de pesticida antiguamente, pero que todavía está presente en el medio ambiente y que, si se introduce en la cadena trófica, puede ser perjudicial para nosotros», aseguraba Kleij, mientras que los ácidos grasos «se encuentran en la naturaleza en la basura». Así, y tal como explicaba el investigador, si estos residuos simplemente se tiran, pierden valor; «pero si se pueden reutilizar, dándoles un valor añadido, diseñas un proceso de economía y química circular sostenible». «Este es el objetivo al cual queremos llegar, lo que se considera una basura con poco valor, lo convertimos en productos reciclados, los cuales seguramente pueden escalar en el interés por parte de los mercados», remarcaba.
En este sentido, los investigadores insisten en entrar en una economía circular sostenible a través de la química verde. Así, lo que tienen presente son los «productos que se puedan reciclar otra vez con un proceso de catálisis», de manera que se transforma en un recurso renovable infinito. Kleij espera que en los próximos años la industria dé apoyo a proyectos como el de TRIPyr y que este tipo de productos escalen en el mercado, pero asegura que es un aspecto que está condicionado totalmente a las empresas. «Depende de qué cosas quieran hacer, qué aplicaciones quieran tener en el mercado. Por ahora, ya hemos firmado un nuevo proyecto con una gran empresa, que nos permitirá trabajar en paralelo este campo de la catálisis,» apuntaba el químico.
El proyecto ha sido cofinanciado en un 65% por el Fondo Europeo de Desarrollo Regional (FEDER) a través del Programa Interreg V-A España-Francia-Andorra (POCTEFA 2014-2020).
Projet réalisé avec le soutien financier de l’Union Européenne.
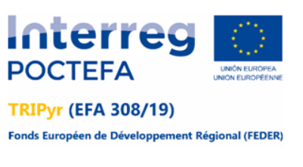
8 décembre 2020
Chemical technologies for the valorization
of industrial wastes in the Pyrenees
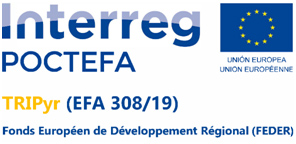 |
Acronym: TRIPyr
Project timespan: April 2020- May 2022
Project leader: Pr. Montserrat Gómez
|
TRIPyr is an interregional European project aiming at developing innovative catalytic technologies towards the transformation of two types of waste: fatty residues arising from the food industry and residues of lindane, a highly toxic pesticide stored in large quantities in the Pyrenees. For this, the project relies on a circular economy concept, in which the generated waste is used as raw material, for the production of high value-added products used in the material sector or fine chemical and medicinal chemical sectors.
TRIPyr is also committed to train young researchers in the development of environmentally friendly processes, and to inform the society about Green Chemistry, its principles and their applications in the waste treatment.
To achieve these multiple objectives, the TRIPyr Consortium is made up of 7 partners (6 beneficiaries and 1 associated partner) coming from Nouvelle-Aquitaine, Aragón, Catalonia, Navarra and Occitanie: the “Laboratoire Hétérochimie Fondamentale et Appliquée” (LHFA-CNRS, Toulouse, Project Coordinator), the “Institut Català d’Investigació Química” (ICIQ, Tarragona), the “Maison Européenne des Procédés Innovants” (MEPI, Toulouse), the “Asociación de la Industria Navarra” (AIN, Cordovilla), the Ecocene association (Pau), the PME Sapoval (Albi) and the “Instituto de Síntesis Química y Catálisis Homogénea” (CHESO, Zaragoza).
Our expected results:
- Use of new catalysts: organocatalysts and (nano)catalysts of abundant and inexpensive metals;
- Synthesis of acids, amines and alcohols from fatty residues;
- Synthesis of polymers from lindane and fatty residues, including activation of CO2;
- Use of flow technologies to achieve greener processes and ease scaling-up.
The purpose of this project is to contribute to the protection of the environment by promoting the life cycle of waste and toxic products, and boosting the economy of the trans-Pyrenean regions.
The project has been 65% co-financed by the European Regional Development Fund (ERDF) through the Interreg V-A Spain France Andorra programme (POCTEFA 2014-2020). POCTEFA aims at reinforcing the economic and social integration of the French–Spanish–Andorran border. Its support is focused on developing economic, social and environmental cross-border activities through joint strategies favouring sustainable territorial development.
Project cofinanced by ERDF
Projet réalisé avec le soutien financier de l’Union Européenne.
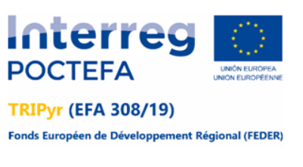
28 juillet 2020
It involves 6 actors from the Pyrenees area both from industry and academic fields, targeting industrial wastes recycling thanks to eco efficient technologies ». « We are delighted to be part of this ambitious project both recognising the expertise of MEPI in innovation & flow chemistry, and servicing the growing need of our society for greener processes ».
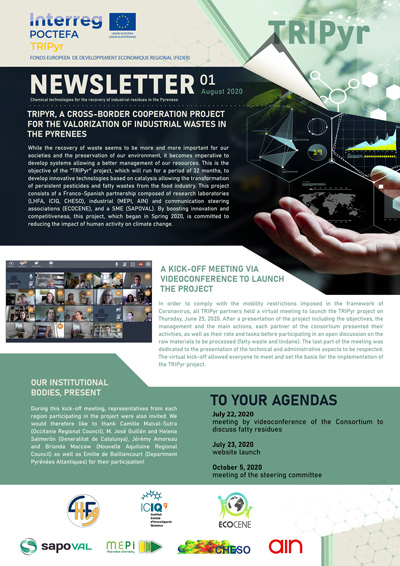
Clic to download
26 février 2019
MEPI attended the Group for Research on Automated Flow and Microreactor Synthesis (GRAMS) symposium on February 8th in Osaka, Japan.
The symposium is organized by the Kinka Chemical Society, and chaired by Professor Jun-ichi Yoshida, a world leader in flow chemistry.
Laurent PICHON, Chairman of MEPI gave a review of MEPI business model, alongside with presentations of success cases of flow chemistries at industrial scale.
The speech was followed by an interactive discussion with the audience.
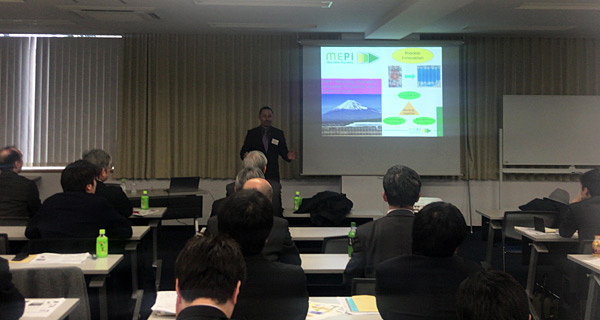
27 novembre 2018
Laurent PICHON, Chairman of MEPI gave an overview of the evolution of the flow chemistry markets over the last decade.
The symposium was organized by TKS.
The presentation is available on request. We are awaiting your mail at : l.pichon@mepi.fr
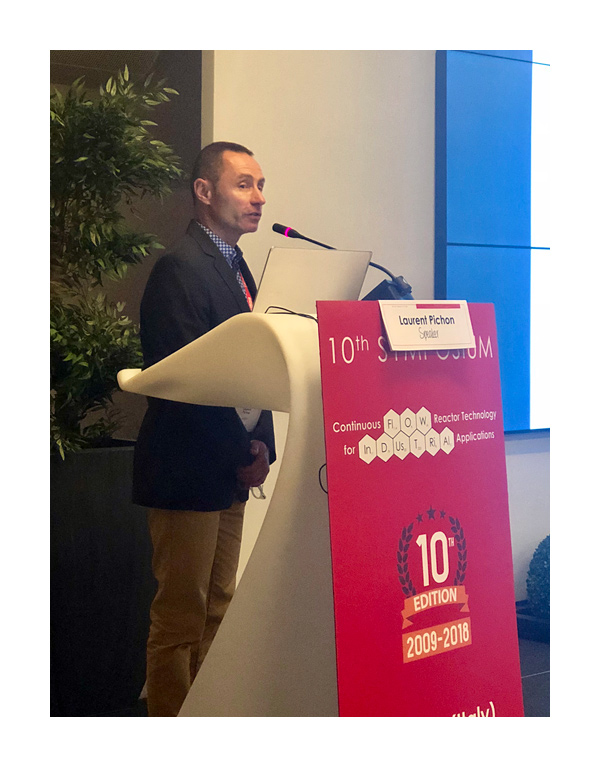
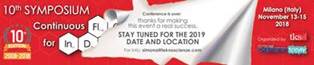

18 avril 2018
MEPI at CPHI Japan 2018, Tokyo April 18th – 20th:
MEPI will attend CPHI Japan 2018.
We’ll be at DKSH, BOOTH F04.
Please contact :
DKSH
Tsuyoshi Takeuchi
DKSH Japan K.K.
3-4-19, Mita, Minato-ku, Tokyo 108-8360, Japan
Phone +81-3-5441-4525, Fax +81-3-5441-4527
Tsuyoshi.Takeuchi@dksh.com
A lecture on flow chemistry will be given by Laurent PICHON, president of MEPI, on Friday April 20th at 11.45.
https://www.ubmjapan-group.com/cphi/en/seminar/index.php?page=pst&DispId=DSP001
18 avril 2018
Overview
SELECTBIO is delighted to welcome you all at the 6th International Conference Flow Chemistry India 2018 to be held on January 17-18, 2018 in Mumbai under the auspices of the Flow Chemistry Society. The society aims to unite and represent those who are actively working on this rapidly developing field. This meeting is dedicated to the integration of flow chemistry into everyday practice throughout the world by delivering the latest knowledge and making it available for the entire chemistry community.
Society individual members save 25% on the registration fee and non-members will receive their first year’s membership included in the fee.
Running alongside the conference will be an exhibition covering the latest technological advances in the area of flow chemistry.
Read the full article HERE
2 février 2017
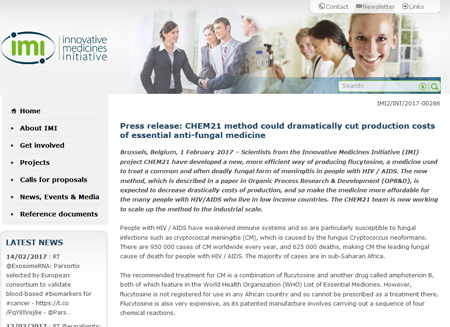
Read here :
http://www.imi.europa.eu/content/chem21-flucytosine
27 janvier 2016
MEPI is exhibiting at INFORMEX , New Orleans (USA) from 2nd to 4th of February 2016.
Join us on the LIBRAGEN booth N° 1024. LIBRAGEN is one of the founding members of MEPI.
This make a unique opportunity to combine your biocatalysis and process intensification needs (microreactors) !
Contact : Laurent PICHON, l.pichon@mepi.fr , Tel. : 00 33 673999531
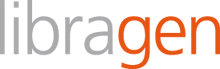
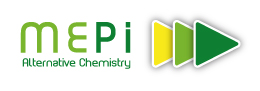
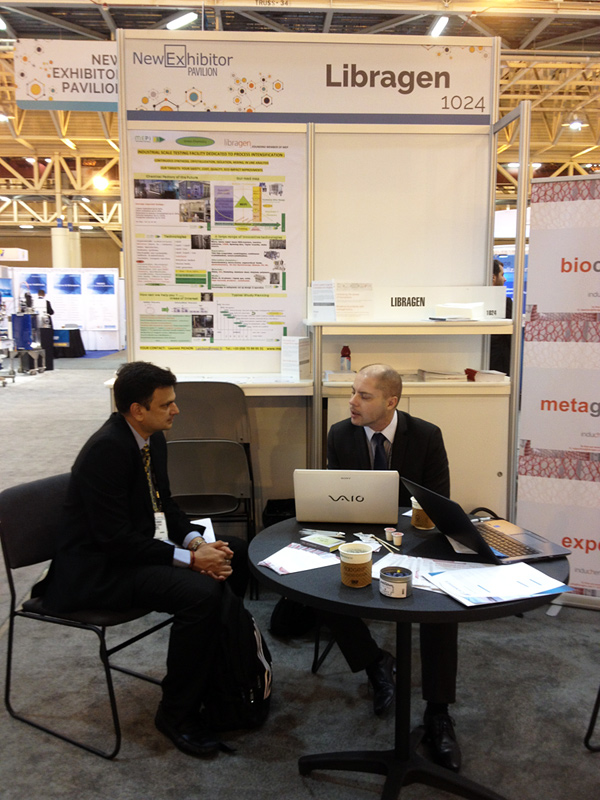
16 novembre 2015
Introduction
Since the last decade, Process Intensification opens up interesting perspectives for the Fine Chemical and Pharmaceutical industries. A wide range of chemistries has been investigated through the use of flow reactors showing the advantages and the improvements related to such technologies, with regards to quality, safety, competitiveness and eco-impact. In this way, various equipments based on the tubular or the heat-exchanger concepts have been developed. All these equipments benefit from miniaturization techniques and micro (or milli)-fluidics to enhance transfer phenomena. Flow reactors are devices where chemical reactions are performed in narrow channels involving a very high surface area to volume ratio which provides very efficient rates of mass and heat transfer. Such key advantages offer new opportunities for preparative photochemistry, like extensive penetration of light, even for concentrated chromophore solutions, decrease of side reactions or decompositions and easy control of the irradiation time. As a consequence, in the last years, there is an increasing interest in flow photochemistry either for producing at lab scale quickly and selectively few milligrams of target molecules (1-4), or for understanding and modelling the positive effects of the small-scale for smart scale-up purposes (5-6). Most of these flow photochemistry studies use “home-made” equipments, i.e. involving non-optimal combinations of flow reactors and light sources. The related results have strengthened this technology breakthrough and driven the development of dedicated flow photo-reactor modules. These commercial solutions mainly focus on the photochemistry development at lab scale (7-10), restricting the scale-up of the considered applications. Few equipments are available at meso scale, i.e. allowing dozens of grams synthesis (11-15): the emergence of the Corning G1 Photo Reactor on the market thus appears as a real opportunity to address this need.
Material and methods
Reactor and facility
The purpose of this work is to assess the potentiality of the Corning technology to perform flow photochemical synthesis at pilot or industrial scale. Corning offers efficient solutions for flow chemistry (Advanced-Flow™ reactors), based on the concept of plate heat-exchangers. These reactors, made of glass, offer at meso-scale a complex design called Heat Exchange and Advanced Reaction Technology (HEART) ensuring enhanced heat and mass transfer (16). A long list of success stories (17- 23) has made them standard tools for process development and continuous production. Hence, the coupling with light sources appears very natural to perform photochemistry while benefitting from performance capabilities of Advanced-Flow™ reactors. Therefore, the resultant Corning G1 photo reactor (see on Figure 1) presents an Advanced-Flow™ design equipped with energy-efficient light sources (LED array), enabling to provide a homogeneous and intense light distribution inside the whole volume (24).
The light source consists in LED arrays placed on both sides of glass fluidic modules and adjustable in terms of wavelength and of light intensity. The wavelengths available are at present limited to 365 nm or 405 nm, which prevents the implementation of photochemical reactions requiring UVB or even UVC light. The reactor conception keeps the versatility and modularity features of Corning reactors by proposing an independent control of the different LED arrays and the possibility of connecting up to 5 fluidic modules in series. The nominal flow-rate range is from 10 to 150mL/min with a maximal allowable pressure inside the channel up to 18 bars. The fluidic module volume, Vr, is 9mL, and the channel depth (in the light attenuation direction) 1.2 mm. For each fluidic module, the irradiated channel surface, Sirrad, is equal to 78cm2.
This work has been carried out at MEPI, a piloting and demonstration facility in Process Intensification (25). To operate under fully controlled operating conditions, a specific module dedicated to continuous applications has been used. This equipment combines dosing lines based on Cetoni NEMESYS syringe pumps and a full data acquisition system on temperature, pressure, flow-rate and density. In the present experiments, typical flow-rates range from 1 to 30mL/min, which corresponds to 0.3 to 9 min of residence time under light irradiation (i.e. of irradiation time). In the case of the 5 fluidic module set-up, a micro gear pump (HNP MZR 7255) in combination with a mass flow controller (Bronkhorst CORI-FLOW™) were used with a typical flow range of 20-200 mL/min.
Reaction
The photochemical reaction under test is the synthesis of pentacyclo(5.4.0.02,6.03, 10.05, 9)undecane-8,11-dione 2 (the ‘cage’ compound, species 2) via the intramolecular (2+2)-photocycloaddition of 1,4,4a,8a-tetrahydro-endo-1,4-methanonaphthalene-5,8-dione 1 (species 1, 174.2g.mol-1), as described on Figure 2. The species 1 is either prepared through a Diels-Alder reaction involving cyclopentadiene and 1,4-benzoquinone (26), or purchased directly (CAS: 51175-59-8). The solvent is ethyl acetate (AcOEt). As shown by (5), the Napierian molar absorption coefficient of the species 1 at the irradiation wavelength (365 nm) is equal to k1=142.2 m2.mol-1, and the species 2 does not absorb significantly at this irradiation wavelength.
Different initial concentrations in species 1, C0, are carried out: 0.1, 0.14 and 0.27mol.L-1. They respectively correspond to Napierian absorbances A0 ranged from 1.7 to 4.6
(1)
Where h is the channel depth in the light attenuation direction (1.2 mm).
Samples are taken at the exit of the photoreactor and stored in the dark in a refrigerator. Then, the solvent is removed under reduced pressure and conversion X is determined by 1H-NMR in CDCl3.
Light conditions are modulated depending on the experiments carried out; thus, the incident light flux density per fluidic module Fwall, is set
- At 40mW.cm-2 when C0was equal to 0.14 and 0.27mol.L-1,
- At 90mW.cm-2 when C0was equal to 0.1mol.L-1.
These incident photon densities correspond to an incident photon flux, qp, (per fluidic module) equal to 3.1W and to 5.5W respectively (which is equivalent, at 365nm, to 34.3mmol photon.h-1 and to 77.1mmol photon.h-1 respectively).
Results and discussion
One of the main issues of continuous intensified reactors (and therefore of continuous photoreactors) lies in residence time. In fact, from hydrodynamics considerations, the flow-rates required to generate high mass and heat transfer rates are directly fixed by the reactor geometry through flow velocity. Thus, there is a minimum flow velocity, generally about 0.1m.s-1 (which is related to the channels dimension), that makes difficult to combine high residence time with efficient performances. Consequently, in such kind of reactors, the residence time is generally restricted to 20 minutes at maximum. Two strategic approaches are then developed to overcome this constraint and carry out slow reactions. A classical approach lies on increasing the residence time by close loop operating, at the expense of productivity. A more innovative approach proposes to reduce the reaction time by modifying operating conditions while profiting of enhanced performances in terms of mixing, heat and mass transfer and light distribution in photoreaction cases. Corning photoreactor is based on this latter concept and the results on the benchmark photoreaction show that its performances allow full conversion to be achieved in less than 10 minutes, whatever the initial concentration was (3 min, 4.5 min and 9 min are respectively required for C0 = 0.1, 0.14 and 0.27mol.L-1). At full conversion, the resultant productivity (averaged over the three initial concentrations) is also significant as 2.96 ± 0.16g.h-1 of “cage” compound can be obtained at reactor outlet.
Regarding the photoreaction performances, a more detailed analysis has been performed to understand the reactor behaviour and to propose a simple methodology for optimal control. Thus, in Figure 3 are reported the variations of the conversion X into species 2, as a function of the irradiation times, tirrad, for different initial concentrations in species 1, C0. For a fixed irradiation time, conversion decreases with increasing initial concentrations. This can be explained by the fact that the light attenuation along the photoreactor depth is stronger when concentrated solutions are involved. Figure 3 also shows that, whatever the initial concentration, few minutes are enough to achieve complete conversion.
For the lowest initial concentration (0.1mol.L-1), the experiments have been carried out using either one or five fluidic modules (noticed FM). As observed in Figure 3, the performances are kept almost constant while increasing the number of fluidic modules, thus emphasizing that the related hydrodynamics modifications inside the reactor channel (in terms of pressure drops and flow behaviour) have a few impact on the conversion achievement. It offers interesting opportunities to increase productivity: at least, a factor 5 could be obtained on the amount of “cage” compound produced by increasing global flow-rates or by using all 5 modules in-parallel. Moreover, in cases where a single module achieved incomplete conversion within the 9 min window, the 5 modules in-series configuration may offer the opportunity to reach full conversion.
Aillet et al (5-6) have proposed a simple modelling approach to describe the coupling between photochemical kinetics, mass, momentum and radiative transfer equations inside flow photoreactors. Assuming a plug-flow behaviour, this model allows predicting the conversion X at the photoreactor outlet with the irradiation time, according to:
(2)
Where A0 is the Napierian absorbances defined by Eq. (1), qp the incident photon flux and Vr the photoreactor volume. The application of this model to the experimental data supposes that the quantum yield of the reaction, Φ, is known. As it is not the case (no value being reported in the literature), the product Φ.qp is directly determined by fitting Eq. 2 with experimental measurements. One obtains a value close to 64.8mmol.h-1 for C0 equal to 0.10mol.L-1 and to 32.4mmol.h-1 for C0 equal to 0.14 and 0.27mol.L-1. When divided by the incident photon flux qP (see values in the section Material and Methods), this leads to a quantum yield slightly smaller than one, as expected for this kind of photochemical reaction.Figure 3 shows that the predicted and measured conversions are in good agreement, and thus Eq. (2) can be used as a tool for predicting the irradiation times required to achieve full conversion for this type of photochemical reaction. From the data reported in Figure 3, one finds some values of Space-Time-Yields from 350 to 600g.L-1.h-1, depending on the initial concentration: they are almost ten times higher than the ones obtained by Aillet et al (5) in a batch immersion well reactor.
Conclusion
The main result of this work was to demonstrate that novel Corning technologies recently proposed for Process Intensification are suitable for preparative photochemistry. Regarding a benchmark photoreaction, the reactor demonstrates that only few minutes were indeed required to achieve full conversion, even for concentrated solutions. In addition, the productivity capabilities were demonstrated through the use of up to 5 fluidic modules set-up in-parallel or in-series. In this last configuration, it has been shown that 30g.h-1 of “cage compound” could be easily produced. Furthermore, a methodology and the related modelling tool have been proposed for optimal process design and control. The emergence of this meso photoreactor that proposes such productivity features, offers interesting perspectives in terms of process development and production. The G1 photo reactor then positions itself as a relevant alternative to typical batch photo-reactors and more particularly in the cases of complex multiphase systems where Corning design has already demonstrated significant benefits (27-31).
3 novembre 2015
MEPI joins the 7ème Symposium on Flow Chemistry
for Industrial Applications – Delft, NL, Sept 29th -Oct 1st 2015
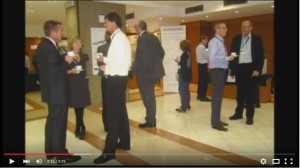
Click here for more details : https://www.youtube.com/watch?v=SAw3w4wylgQ
4 mars 2015
After the really big success of the first five symposia held in Madrid, Paris, Como, Lisbon and Pisa, Chimica Oggi/Chemistry Today, TKS Publisher, organized in Budapest the sixth symposium on « Continuous Flow Reactor Technology for Industrial Applications ». The symposium was held on September 23-26 and had a new improved format…
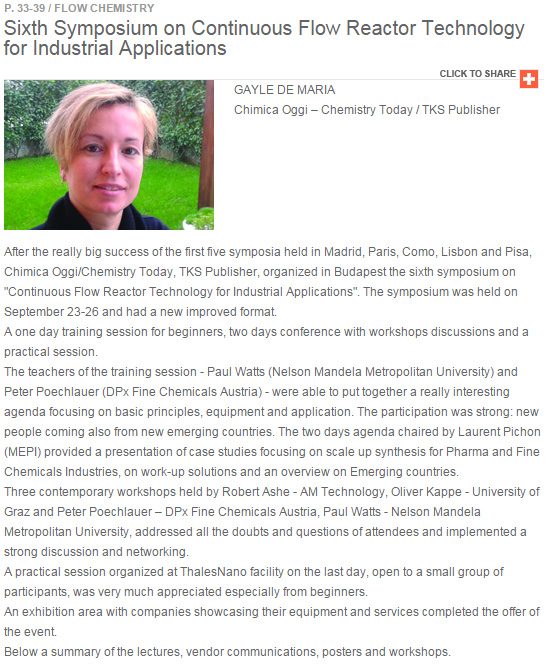
Read the full article
5 novembre 2014
Continuous lipase esterification using process intensification technologies
http://onlinelibrary.wiley.com/doi/10.1002/jctb.4247/abstract
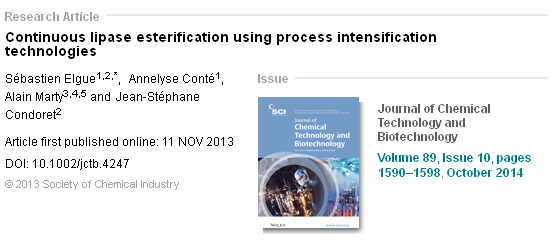
31 octobre 2014
Safer, Greener, Faster and Cheaper
Manufacturing is now a key area for companies as they reduce costs and increase their flexibility to respond to changing market needs.
NiTech’s new DN15 range of continuous crystallisers and reactors is designed to meet today’s manufacturing challenges.
Our new Newsletter highlights the individual laboratory-scale products now available, which start from £45000.
It also provides details of the proof-of-concept and feasibility services offered by our European partner laboratories – SP Process Development in Sweden, and MEPI in France.
Please click here to download your copy of the Newsletter.
Paul Hodges
Chairman
NiTech Solutions Limited
www.nitechsolutions.co.uk
28 octobre 2014
Another big success for Chimica Oggi – Chemistry Today, organizer of the 6th Symposium on Continuous Flow Reactor Technology for Industrial Applications
After the really big success of the first five symposia held In Madrid, Paris, Como, Lisbon and Pisa, Chimica Oggi/Chemistry Today, TKS Publisher, organized in Budapest the sixth symposium on « Continuous Flow Reactor Technology for Industrial Applications ». The symposium was held on September 23-26 and had a new improved format.
A one day training session for beginners, two days conference with workshops discussions and a practical session.
The teachers of the training session – Paul Watts (Nelson Mandela Metropolitan University) and Peter Poechlauer (DSM) – were able to put together a really interesting agenda focusing on basic principles, equipment and application. The participation was strong: new people coming also from new emerging countries. The two days agenda chaired by Laurent Pichon (MEPI) provided a presentation of case studies focusing on scale up synthesis for Pharma and Fine Chemicals Industries, on work-up solutions and an overview on Emerging countries.
Three contemporary workshops held by Robert Ashe – AM Technology, Oliver Kappe – University of Graz and Peter Poechlauer –DSM, Paul Watts – Nelson Mandela Metropolitan University, addressed all the doubts and questions of attendees and implemented a strong discussion and networking.
A practical session on the last day open to a small group of participants was very much appreciated especially from beginners.
An exhibition area with companies showcasing their equipment and services completed the offer of the event. This year new companies decided to show up and were met with great participants approval.
Not to forget the bus tour in Budapest with a cruise dinner on the Danube: a fantastic way to break the ice and exchange ideas “in continuous”.
TKS organization is already working on the next event so stay tuned and don’t miss our announcements or go to www.teknoscienze.com to keep up to date.
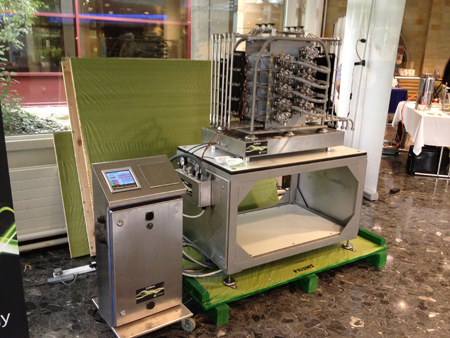
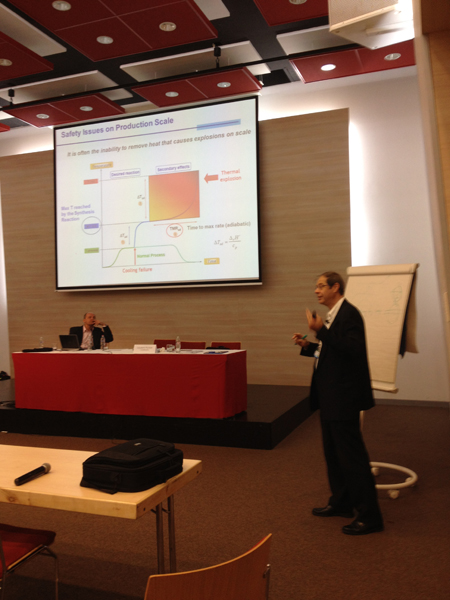
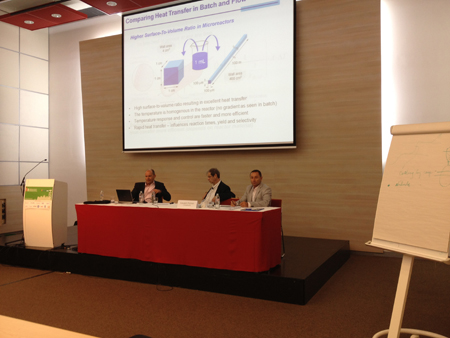
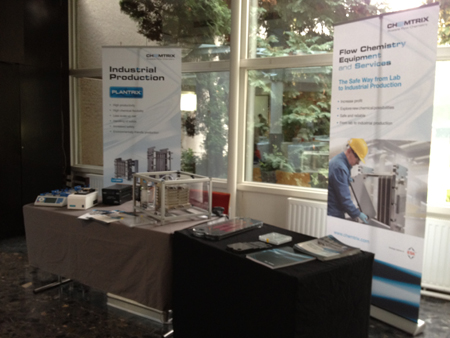
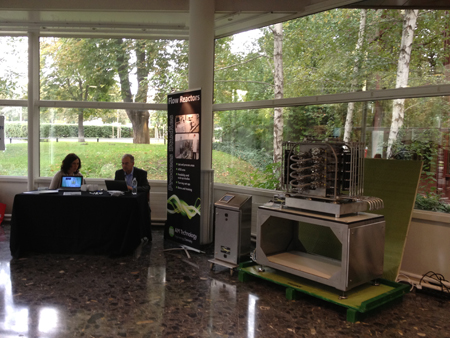
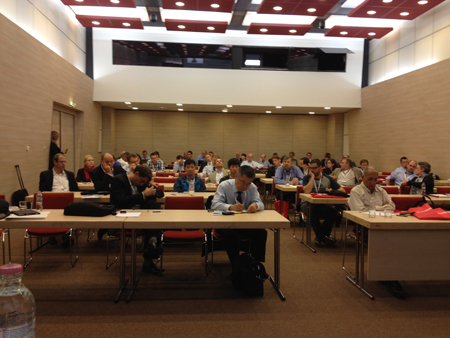
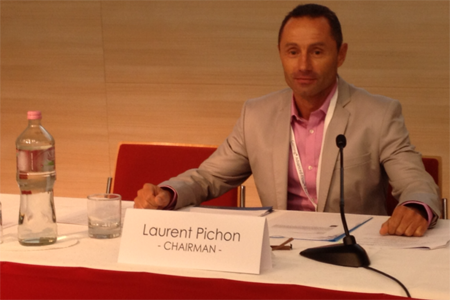
6 octobre 2014
MEPI was exhibiting, with the local Green Chemistry Cluster, at the 1st International Connecting Show (ICS),
held in Toulouse from the 17th to the 19th of September 2014.
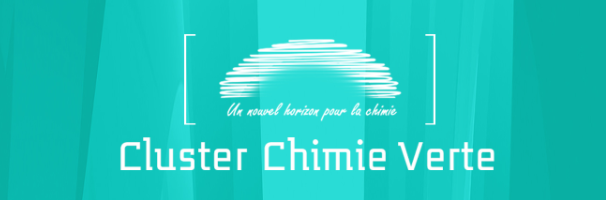
12 juin 2014
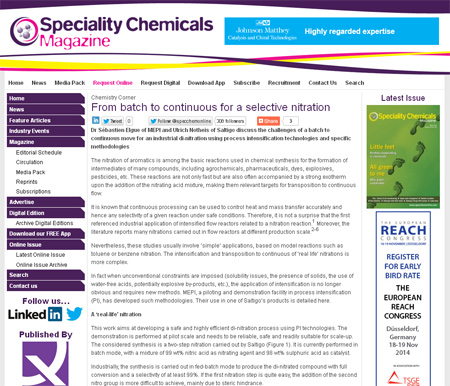
Read the article in details
4 octobre 2013
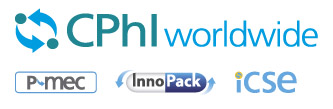
MEPI is attending CPHI 2013 held at the Frankfurt Messe, Germany, from the 22nd to the 24th of October 2013. We’ll be pleased to discuss our offer, news, and review your projects on this occasion.
Please fill your MEPI contact details to arrange appointment. We look forward to seeing you shortly in Frankfurt !
6 mars 2013
MEPI presents the results of a market study on flow chemistry at the 4th symposium on Continuous Flow Reactor Technology for Industrial Applications in Lisbon.
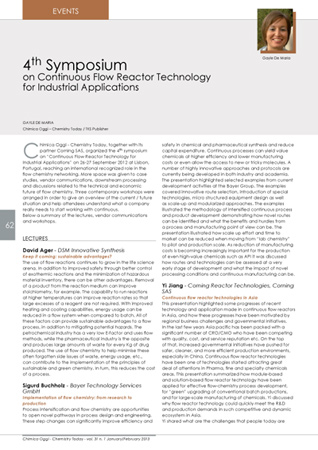
Read more
30 août 2012
MEPI is attending CPHI 2012 held at the Madrid Feria, Spain, from the 9th to the 11th of October 2012. We’ll be pleased to discuss our offer, news, and review your projects on this occasion.
Please fill your MEPI contact details to arrange appointment. We look forward to seeing you shortly in Madrid !
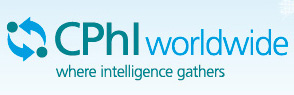
27 août 2012
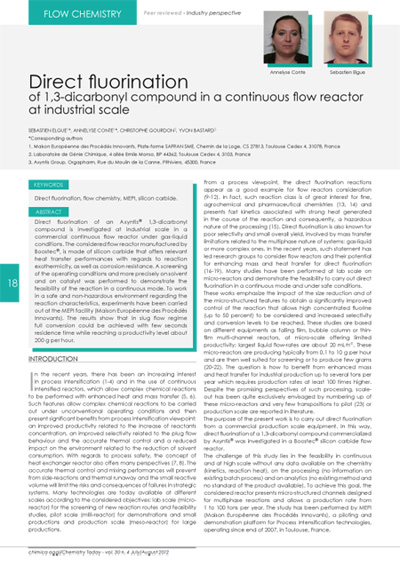
More détails here
29 juin 2012
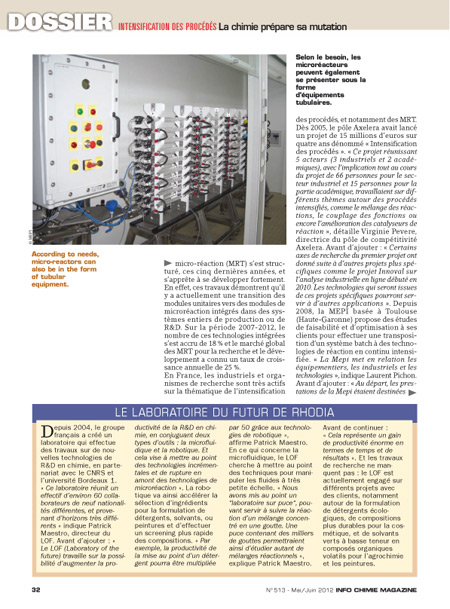
You can read this article in details here
15 mai 2012
MEPI is attending IPIT 2012 held in Rotterdam, The Netherlands, on Friday May 25th. On this occasion, Laurent PICHON, Business Director of MEPI shall present “INNOVATIVE SOLUTIONS FOR THE FLOW CHEMISTRY EXPECTATIONS IN EUROPE”
We look forward to seeing you shortly in Rotterdam !
More information : www.tno.nl

15 mai 2012
MEPI is attending ACHEMA 2012 at the Messe exhibition Center, Frankfurt, Germany, on the 19th and 20 th of June 2012. We’ll be pleased to discuss our offer and review your process intensification projects on this occasion. Please fill your MEPI contact details in to arrange appointments.
We look forward to seeing you shortly in Frankfurt !
More details : http://www.achema.de/
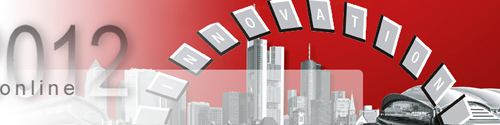
15 mai 2012
MEPI is attending CHEMSPEC 2012 held at the Gran Via exhibition Center, Barcelona, Spain, on the 13th and 14 th of June 2012. We’ll be pleased to discuss our offer and review your process intensification projects on this occasion. Please fill your MEPI contact details in to arrange appointments.
We look forward to seeing you shortly in Barcelona !
More details : http://www.chemspecevents.com/europe/

2 mars 2012
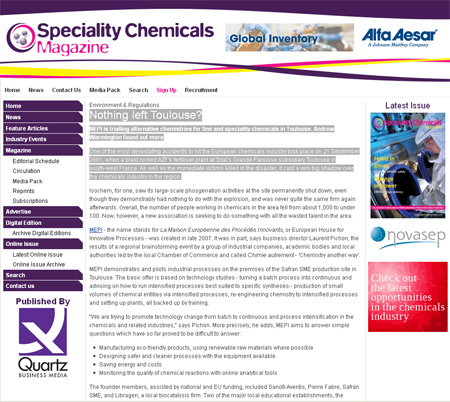
Nothing left Toulouse?
MEPI is trialling alternative chemistries for fine and speciality chemicals in Toulouse. Andrew Warmington found out more
One of the most devastating accidents to hit the European chemicals industry took place on 21 September 2001, when a blast rocked AZF’s fertiliser plant at Total’s Grande Paroisse subsidiary Toulouse in south-west France. As well as the immediate victims killed in the disaster, it cast a very big shadow over the chemicals industry in the region.
Read more
7 novembre 2011
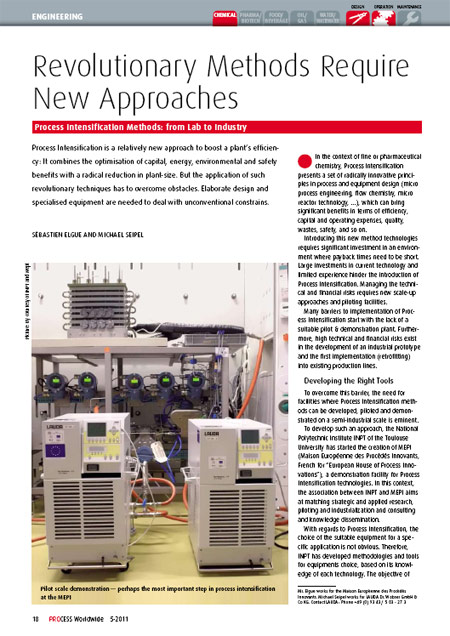
Read more
27 septembre 2011
MEPI is attending CPHI 2011 held at the Messe Frankfurt, Germany, from the 25th to the 27th of October 2011.
We’ll be pleased to discuss our offer, news, and review your projects on this occasion.
Please fill your MEPI contact details to arrange appointment.
We look forward to seeing you shortly in Frankfurt !
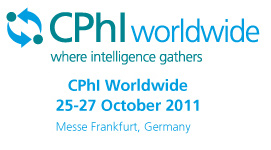
27 septembre 2011

Following the AZF fertilizer plant blast in 2001, a brain-storming group was formed in Toulouse, France, to draw the lines of what would in 2007 become MEPI, la Maison Européenne des Procédés Innovants.
Read more
9 mai 2011
MEPI is attending CHEMSPEC 2011 held at the Hall 1 Palexpo, Geneva, Switzerland, on the 15th and 16 th of June 2011. We’ll be pleased to discuss our offer and review your process intensification projects on this occasion. Please fill your MEPI contact details in to arrange appointments.
We look forward to seeing you shortly in Geneva !
More details : http://www.chemspecevents.com/europe/

13 octobre 2010
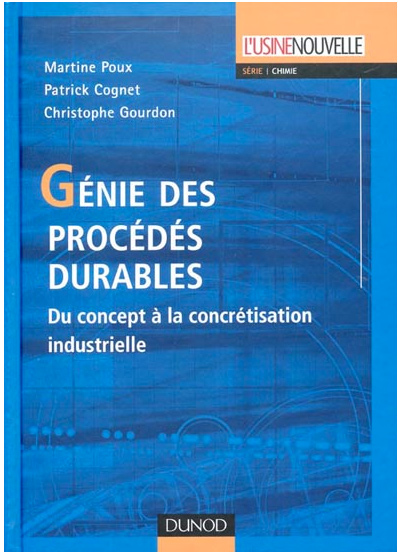
recently published by Dunod. This is the first French publication on this topic!
This book has been coordinated by Martine POUX, Patrick COGNET and Christophe GOURDON from the Laboratoire de Génie Chimique/ENSIACET, Toulouse. It presents an ensemble of methods and new chemical engineering routes that can be integrated in industrial processing for safer, more flexible, economical and ecological production processes in the context of green and sustainable engineering.
Different methods for improving process performance are dealt with, including:
– eco-design and process optimization by systemic approaches
– new technologies for intensification
– radical change of industrial processes via the use of new media and new routes for chemical synthesis.
These various methods are fully illustrated with examples and industrial cases, giving this book a much applied nature. It is particularly recommended for technicians and engineers, as well as university students and professors.
More details here
27 juillet 2010
« This agreement brings MEPI additional technologies and confirms its commitment towards Innovative intensified Processes.
This will contribute to widden its equipments portfolio, in compliance with its development program and allows MEPI to answer the technological challenges brought by its increasing number of clients. » added Laurent PICHON, in charge of MEPI business development.
More details HERE (La Dépêche du Midi du 25/07/10).
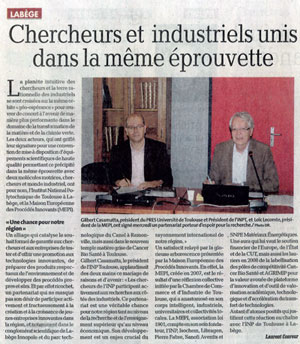
27 juillet 2010
MEPI is attending the Chemistry Today Corning Continuous Flow Reactor Technology for Industrial Applications 2010 that will be held just before CPHI at the Espaces CAP 15 Centre International d’Affaires et de Congrès, Paris, from the 3rd to the 4 th of October 2010.
We’ll be pleased to discuss our offer and review your projects on the occasion.
Please fill your MEPI contact details to arrange appointment.
We look forward to seeing you shortly in Paris !
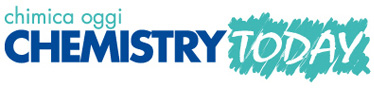
27 juillet 2010
MEPI is attending CPHI 2010 held at the Villepinte Exhibition Center, Paris, from the 5th to the 7th of October 2010.
We’ll be pleased to discuss our offer and review your projects on the occasion.
Please fill your MEPI contact details to arrange appointment.
We look forward to seeing you shortly in Paris !
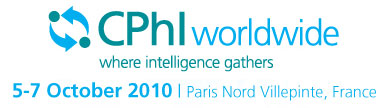
23 avril 2010
MEPI is attending CHEMSPEC 2010 held at the Messe Berlin, Germany, on the 9th and 10 th of June 2010.
We’ll be pleased to discuss our offer and review your projects on the occasion.
Please fill your MEPI contact details to arrange appointment.
We look forward to seeing you shortly in Berlin !

25 mars 2010
MEPI attented the 13th Cathala Letort seminar « Separation processes : the new challenges of life sciences » (18,19th March 2010, Nancy, ENSIC).
15 mars 2010
2nd European Process Intensification Conference on 14-17 june 2009 – Venice (Italy)
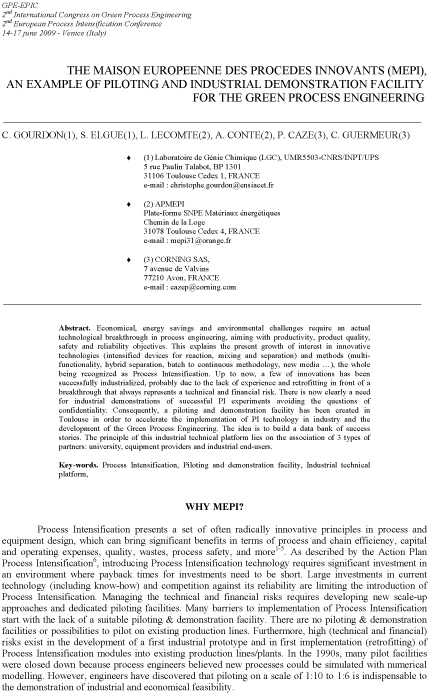
Read the full pdf here
10 février 2010
Welcome to www.mepi.fr
Stay tuned !